一、模貝溫度的影響。注塑加工成形中的溫度以模貝溫度對制品規(guī)格精密度影響很大。模貝溫度是根據(jù)熔化態(tài)高分子的趨向與結晶度大小,立即影響制品收縮率轉變,進而引起規(guī)格偏差。
I. The Influence of mould temperature. The mold shell temperature has a great influence on the specification precision of products in injection molding. The mold shell temperature immediately affects the shrinkage change of the product according to the trend and crystallinity of the molten polymer, and then causes the specification deviation.
針對非結晶形樹脂,模溫高,溶體冷卻慢,分子有充足的松馳時間,結晶趨向更完整,結晶度高,使收縮增加。 但對結晶形樹脂,注塑加工全過程中,高模溫可減少后收縮,使制品規(guī)格平穩(wěn)。
For the amorphous resin, the mold temperature is high, the cooling of the solution is slow, the molecules have sufficient relaxation time, the crystallization tends to be more complete, the crystallinity is high, and the shrinkage increases. However, for crystalline resin, in the whole process of injection molding, high mold temperature can reduce post shrinkage and make the product specification stable.
模溫低,則制冷快,溶體分子結構被凍潔趨向趕不及松馳,不容易結晶體,容積轉變小,制品收縮小。但低模溫使制品后收縮增加,收縮時間延長,不容易平穩(wěn)注塑加工件的規(guī)格。 溫度是結晶體全過程中比較敏感的要素,溫度差1℃結晶體速率可相距好幾倍。模貝溫度不勻或不穩(wěn)定,立即影響結晶度大小尺寸,進而使注塑加工制品收縮造成規(guī)格偏差。
If the mold temperature is low, the refrigeration is fast, the molecular structure of the solution tends to be frozen and cleaned, and it is not easy to relax, the crystal is not easy, the volume transformation is small, and the shrinkage of the product is small. However, low mold temperature increases the post shrinkage of products and prolongs the shrinkage time, which is not easy to stabilize the specification of injection molded parts. Temperature is a sensitive factor in the whole process of crystallization. The crystallization rate can be several times with a temperature difference of 1 ℃. Uneven or unstable mold shell temperature will immediately affect the crystallinity and size, and then shrink the injection molded products, resulting in specification deviation.
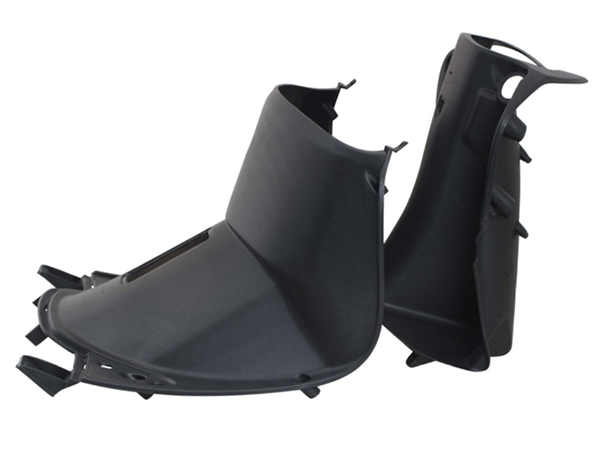
二、打針壓力的影響。打針壓力的變化導致制品尺寸的顛簸。其它注塑加工工藝參數(shù)不變時,進步打針壓力,可改善熔體充?;顒有?,增加活動長度,充模速度加快,制品密實,收縮減小,但易產生取向應力。壓力低時,制品得不到充分壓實,收縮加大。
2、 Effect of injection pressure. The change of injection pressure leads to the fluctuation of product size. When other injection molding process parameters remain unchanged, increasing the injection pressure can improve the melt filling activity, increase the active length, accelerate the filling speed, compact the product and reduce the shrinkage, but it is easy to produce orientation stress. When the pressure is low, the product can not be fully compacted and the shrinkage increases.
三、保壓壓力的影響。保壓壓力對穩(wěn)定制品尺寸有重要作用,在注塑加工過程中,進步保壓壓力,可對模內制品的收縮進行補料壓實,減小收縮。但保壓壓力太高,會造成制品脫模時的殘余應力增大,惹起變形或開裂,影響制品尺寸。
3、 Effect of holding pressure. The holding pressure plays an important role in stabilizing the size of products. In the process of injection molding, increasing the holding pressure can supplement and compact the shrinkage of products in the mold and reduce the shrinkage. However, if the holding pressure is too high, it will increase the residual stress during demoulding, cause deformation or cracking, and affect the size of the product.
四、打針時間的影響。在澆口關閉前,打針時間越短,收縮率越大,并且收縮率的變化幅度也越大;當打針時間達到或超過澆口的凝固時間時,即使再延長打針時間,注塑加工制品質量和收縮率也不再發(fā)生變化,打針時間控制與所設計的澆口厚度關系親切,澆口厚度能夠在非常大程度上左右澆口關閉時間。
4、 Effect of injection time. Before the gate is closed, the shorter the injection time is, the greater the shrinkage is, and the greater the change range of shrinkage is; When the injection time reaches or exceeds the solidification time of the gate, even if the injection time is extended, the quality and shrinkage of injection molded products will not change. The injection time control has a close relationship with the designed gate thickness, and the gate thickness can control the gate closing time to a great extent.
五、保壓時間的影響。保壓時間越長有利于熔體補塑壓實,注塑加工件密度越大,收縮率越小。當澆口凝封后,保壓對注塑加工制品收縮的減小不復興作用,過長的保壓時間會延長成型周期。
5、 Influence of holding time. The longer the holding time is conducive to the plastic filling and compaction of the melt. The greater the density of the injection molded parts, the smaller the shrinkage. When the gate is sealed, the pressure holding has no effect on the reduction of shrinkage of injection molded products, and too long pressure holding time will prolong the molding cycle.